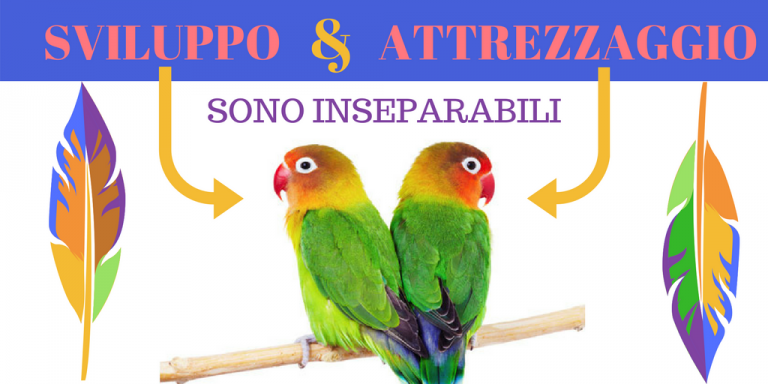
Torniamo a parlare di sviluppi della lamiera:
Purtroppo, però, c’è da dire che la differenza tra ciò che vorrei ottenere e ciò che poi ottengo, è un problema veramente spinoso e che va affrontato necessariamente se abbiamo a cuore la qualità dei nostri pezzi.
Siamo consci del fatto che esistono diverse strade per ottenere gli sviluppi più corretti possibile.
Quella più tradizionale, tipica di chi ha “le mani in pasta” tutti i giorni e che prevede che mediante tutta una serie di prove incrociando spessori, materiali e utensili si ricavino dei “numerini” che poi rappresentano le correzioni in millimetri da applicare ogniqualvolta si ripresentino le stesse condizioni.
ESEMPIO
Voglio piegare una “L” di ferro con dimensioni 50×50 millimetri esterne, spessore 30/10 di mm e dispongo di una matrice V=20 a 60°.
Se taglio una prova lunga 94 mm (47+47, che poi sono le misure esterne) noterò che, verosimilmente, mi mancherà poco più di mezzo millimetro in totale per raggiungere la misura da 50×50 precisa.
Quindi, ad esempio, se misurerò il pezzo piegato dalla prova, potrò ottenere 49,7×49,7.
Perfetto!
Nella mia tabella esperienziale segnerò il valore 0,6, che indica la misura in millimetri da aggiungere ogni volta futura che dovrò piegare un 30/10 di ferro con la mia matrice da 20 a 60°
Tutto ok? Non proprio.
Non tutti sanno (solo i più attrezzati) che, per quanto riguarda gli sviluppi della lamiera, quello che è vero per una matrice a 60°, non lo è più se è a 88°, a parità di spessore e materiale.
Eh, già!
Quindi, se dispongo di un pezzo con 8 pieghe a cui ho dato una correzione di 0,6 in quanto è di ferro da 30/10 e verrà piegato in cava da 20 a 60°, mi “mancheranno” circa 2,5mm e oltre sul totale delle misure esterne del pezzo finito.
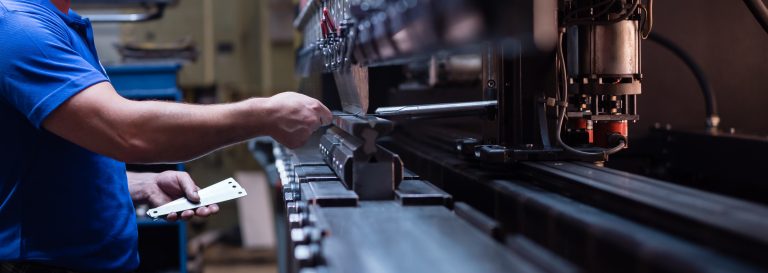
E ALLORA, COME REGOLARSI?
- Con una matrice da 60°, 45°, 30° o in ogni caso con un angolo sensibilmente più “chiuso” di 85 gradi:
si pregiudica il fatto che stiamo piegando “in aria” e ottenendo, quindi, un raggio interno piuttosto dolce.
- Se lavoriamo con una cava da 85 o 88° stiamo piegando “a fondo matrice”:
otteniamo così dei raggi più piccoli e quindi pieghe più secche, minore quantità di fibre coinvolte nella deformazione e in maniera più stressante e, di conseguenza, minore ritorno elastico.
- In coniatura, invece, abbiamo un punzone e una matrice da 90° con un raggio interno di piega ottenuto uguale a quello del punzone.
Come viene approfondito nell’articolo “La magia dei raggi interni“.
C’È PERÒ ANCHE UN ALTRO APPROCCIO CHE DÀ OTTIMI RISULTATI E CHE È PIÙ UTILIZZATO OLTREOCEANO.
Prevede una serie di semplificazioni diverse dalle nostre, o da quelle che spesso vediamo nei nostri regoli di piegatura e un aggiustamento del fattore K in base alla modalità di piega (piegatura in aria, piegatura a fondo matrice e in coniatura).
Si parte innanzitutto dal raggio che non è più inteso come “circa V/8” (come ad esempio una matrice da 16 che genera un raggio interno da 2mm per il ferro e poi corretto x 0,8 per l’alluminio e x1,4 per l’inox Aisi 304), bensì a “percentuale”.
Si, ma quanto? Nel seguente modo:
Per l’inox il raggio interno vale dal 20 al 22% il valore della larghezza della matrice.
Il ferro tra il 15% e 1l 17% e l’alluminio tra 13% e il 15%.
Come si può osservare, più è tenero il materiale, più è piccolo il raggio di piegatura.
Si può semplificare anche dicendo che un materiale che genera un raggio del 13%, un altro avente resistenza a snervamento doppia, genera un raggio di piegatura del 26%.
Bene, ora si tende a “forzare” il raggio alla quota data dal calcolo delle percentuali e considerarlo piuttosto fisso.
Ora, ricordi il concetto di Fattore K? Quel rapporto tra la distanza tra il piano neutro e il raggio interno e lo spessore totale della lamiera?
Per rinfrescare l’argomento, ti invito a leggere l’articolo “Capire il fattore K“.
Secondo questo approccio, è il valore da modificare in base al materiale e al tipo di piegatura.
ESEMPIO
Ho un profilo a “L” da ottenere con misure esterne da 50×50 in ferro 50/10 in matrice da 32 a 60° (quindi con piegatura in aria).
Ricavo il raggio con una percentuale del 16% della larghezza della matrice, quindi r= 5.12
Ora, grazie alla tabella dei fattori k, nella sezione di r compreso tra una e tre volte lo spessore, materiale duro e piegatura in aria, ottengo un k= 0.45
Facendo un semplicissimo calcolo geometrico otterrò il seguente sviluppo:
AB+BC- 2x(r+S)+((0.45xS)+r)x 3,14
2
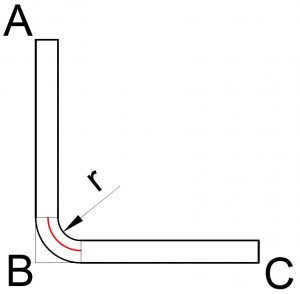
Nulla di diverso, quindi dal solito metodo di:
1) Dividere il pezzo tra tratti dritti e tratto deformato
2) Individuare la lunghezza di ogni tratto dritto, pari alla misura esterna meno lo spessore e il raggio interno
3) Moltiplicare il dato per due (due tratti dritti)
4) individuare la lunghezza del tratto deformato grazie al fattore k e che sarà pari a un quarto di circonferenza (per una piega a 90°) di un raggio lungo r+(k x S) e corrispondente alla lunghezza dell’arco rosso della figura.
5) Sommare il tutto.
Quindi, con i numeri:
50+50-2x (5.12+5) + (0.45×5)+5.12)x3.14
2
Che equivale a 91.3 mm
Tornando, quindi, all’approccio empirico delle tabelle esperienziali, avremmo che un 50/10 di ferro in cava da 32 in aria, necessita di una correzione di 1,3 mm a piega.
Se vogliamo fare la stessa cosa, ma piegando a fondo matrice con una cava, quindi, da 88° e sempre da 32, sostituiremo il fattore k forzando il raggio a 5.12 mm.
Consultiamo di nuovo la tabella dei fattori k che ci dà un valore di 0.48, quindi a parità di raggio, uno sviluppo più lungo.
In un articolo andremo a vedere diversi esempi e nuove cosucce riguardanti lo sviluppo e non solo.
Ma se vuoi anche tu poter avere sviluppi esatti utilizzando questo metodo, non ti resta che ottenere la tabella dei fattori k!
RESTIAMO IN CONTATTO:
SCRIVIMI UNA MAIL ALL’INDIRIZZO EMILIANO@ACCADEMIADELLAPIEGATURA.IT
VISITA IL SITO INTERNET WWW.ACCADEMIADELLAPIEGATURA.IT
LASCIA IL TUO MI PIACE ALLA PAGINA FACEBOOK DI ADP
DIVENTA UN MIO COLLEGAMENTO SU LINKEDIN
ISCRIVITI AL CANALE YOUTUBE